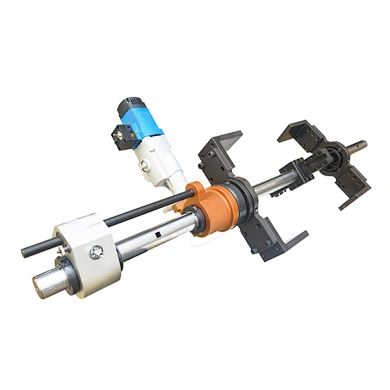
# Industrial Flange Facer: Essential Tool for Precision Machining
## Introduction to Industrial Flange Facers
Industrial flange facers are specialized machines designed to create precise, flat surfaces on pipe flanges. These powerful tools play a critical role in ensuring proper sealing and alignment in piping systems across various industries. From oil and gas to chemical processing plants, flange facers help maintain the integrity of critical connections that handle high pressures and temperatures.
## How Flange Facers Work
Flange facers operate by mounting directly onto the flange face and using cutting tools to machine the surface to exact specifications. The process typically involves:
– Securing the machine to the flange
– Adjusting the cutting tools to the required depth
– Rotating the cutting head to remove material evenly
– Finishing the surface to the desired smoothness
Modern flange facers often incorporate digital readouts and automated features to ensure consistent, high-quality results with minimal operator intervention.
Keyword: Industrial flange facer
## Key Applications in Industry
These versatile machines find applications in numerous industrial settings:
### Oil and Gas Sector
In refineries and pipelines, flange facers ensure proper sealing of high-pressure connections that transport crude oil, natural gas, and refined products.
### Power Generation
Power plants use flange facers to maintain steam and water piping systems that must withstand extreme temperatures and pressures.
### Chemical Processing
The chemical industry relies on precisely faced flanges to prevent leaks of hazardous materials and maintain process integrity.
## Benefits of Using Professional Flange Facers
Investing in quality flange facing equipment offers several advantages:
– Improved safety by ensuring proper flange mating
– Reduced downtime during maintenance and repairs
– Longer service life for gaskets and sealing components
– Cost savings through in-situ machining (no need to remove flanges)
– Consistent results meeting industry standards
## Choosing the Right Flange Facer
When selecting a flange facer, consider these factors:
– Flange size range the machine can handle
– Power source requirements (electric, hydraulic, or pneumatic)
– Portability and weight for field applications
– Available accessories and tooling options
– Precision capabilities and repeatability
## Maintenance Tips for Longevity
Proper care extends the life of your flange facer:
– Clean the machine after each use to remove metal chips and debris
– Lubricate moving parts according to manufacturer specifications
– Store cutting tools properly to prevent damage
– Regularly inspect for wear on critical components
– Follow all safety protocols during operation
## The Future of Flange Facing Technology
As industries demand higher precision and efficiency, flange facer technology continues to evolve. Emerging trends include:
– Integration with digital measurement systems
– Automated tool changing capabilities
– Lightweight composite materials for portable units
– Smart sensors for real-time performance monitoring
– Enhanced safety features for hazardous environments
Industrial flange facers remain indispensable tools for maintaining piping system integrity across countless applications. By investing in quality equipment and proper training, facilities can ensure reliable operation while minimizing downtime and maintenance costs.