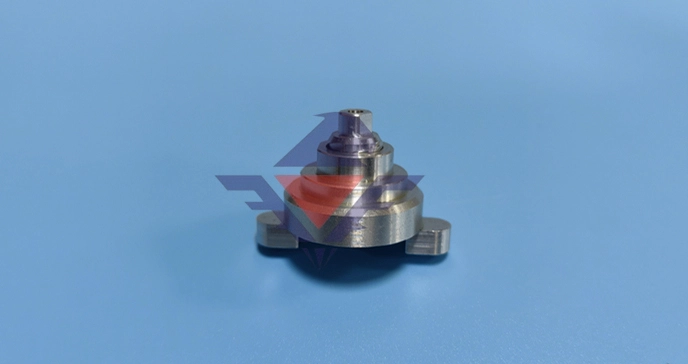
Keyword: Swiss Screw Machining
# Swiss Screw Machining: Precision and Efficiency in Manufacturing
## Introduction to Swiss Screw Machining
Swiss screw machining, also known as Swiss turning or Swiss-style lathe machining, is a highly specialized manufacturing process that has revolutionized the production of small, complex, and precision parts. Originating in Switzerland’s watchmaking industry, this technology has evolved to become a cornerstone of modern precision manufacturing across various industries.
## How Swiss Screw Machining Works
Unlike conventional lathes, Swiss screw machines feature a sliding headstock that moves the workpiece along the Z-axis while the cutting tools remain stationary. This unique design provides several advantages:
– Exceptional precision for small diameter parts
– Reduced vibration during machining
– Ability to maintain tight tolerances
– Improved surface finishes
The guide bushing, a key component of Swiss machines, provides support close to the cutting area, minimizing deflection and enabling precise machining of slender parts.
## Advantages of Swiss Screw Machining
### 1. High Precision Capabilities
Swiss screw machines can achieve tolerances as tight as ±0.0002 inches (0.005 mm), making them ideal for medical devices, aerospace components, and electronics.
### 2. Increased Productivity
The ability to perform multiple operations simultaneously (turning, milling, drilling, threading) significantly reduces cycle times compared to traditional machining methods.
### 3. Material Efficiency
Swiss machining minimizes material waste, especially important when working with expensive materials like titanium or medical-grade alloys.
### 4. Complex Geometries
These machines excel at producing parts with intricate features that would be challenging or impossible to create using conventional methods.
## Applications Across Industries
Swiss screw machining serves numerous industries with its precision capabilities:
– Medical: Surgical instruments, implants, and dental components
– Aerospace: Fuel system components, fasteners, and sensor housings
– Automotive: Fuel injection parts, transmission components
– Electronics: Connectors, contacts, and miniature hardware
– Defense: Firearm components and guidance system parts
## Choosing the Right Swiss Screw Machining Partner
When selecting a Swiss machining provider, consider these factors:
– Experience with your specific industry requirements
– Quality certifications (ISO, AS9100, etc.)
– Material expertise
– Secondary processing capabilities
– Quality control measures
## The Future of Swiss Machining
As manufacturing demands continue to evolve, Swiss screw machining technology is advancing with:
– Integration of automation and robotics
– Improved CNC controls and software
– Enhanced multi-tasking capabilities
– Development of hybrid machines combining Swiss turning with other processes
These innovations ensure Swiss screw machining remains at the forefront of precision manufacturing solutions.
## Conclusion
Swiss screw machining represents the pinnacle of precision manufacturing, offering unparalleled accuracy, efficiency, and versatility for small, complex parts. As industries continue to demand higher precision components with tighter tolerances, Swiss machining technology will play an increasingly vital role in meeting these challenges while maintaining cost-effectiveness and production efficiency.